فرآیند تایید بخش تولید (PPAP) ابزار ارزشمندی برای ایجاد اطمینان در تامین کنندگان قطعات و فرآیندهای تولید آنها است.
در محیط رقابتی تولید امروز، کنترل هزینه و حفظ سطح بالای کیفیت برای موفقیت یک شرکت حیاتی شده است. افزایش هزینه تجهیزات، مواد و نیروی کار همراه با گسترش بازارهای جهانی منجر به افزایش قطعات برون سپاری شده است. بسیاری از قطعات به تولیدکنندگان خارج از کشور واگذار می شوند. این اغلب منجر به زمان طولانی تر و تعداد سفارش بیشتر می شود. بنابراین، ارائه قطعات با کیفیتی که نیازهای مشتری را در اولین بار و هر بار برآورده می کند، ضروری شده است. در ابتدا PPAP توسط صنایع خودروسازی و هوافضا مورد استفاده قرار گرفت. PPAP اکنون توسط چندین صنعت برای بهبود ارتباطات و ارائه محصولات با کیفیت استفاده می شود. در صنعت خودرو، منبع نهایی برای اطلاعات PPAP کتابچه راهنمای منتشر شده توسط گروه اقدام صنعت خودرو (AIAG) است. PPAP (فرایند تایید بخش تولید) توسط AIAG (گروه اقدام صنعت خودرو) توسعه یافته است و بخش مهمی از رویکرد جامع برنامه ریزی کیفیت پیشرفته محصول (APQP) است و برای حمایت از فعالیت های کلیدی و تسهیل همکاری بین تامین کنندگان و مشتریان استفاده شده است.
PPAP فرآیند تایید قطعات جدید یا اصلاح شده یا قطعات تولید شده با روش های تولید جدید یا اصلاح شده را تعریف می کند. فرآیند PPAP شامل 18 عنصر است که ممکن است برای تایید قطعات تولیدی مورد نیاز باشد. همه عناصر برای هر ارسال مورد نیاز نیست. به طور کلی پنج سطح ارائه PPAP پذیرفته شده؛ وجود دارد. کتابچه راهنمای PPAP حاوی اطلاعات دقیق، دستورالعمل ها و اسناد نمونه مفید برای تکمیل الزامات فرآیند است. ارسال PPAP حاصل شواهدی را ارائه میکند که نشان میدهد تامینکننده نیازهای مشتری را برآورده کرده یا از آن فراتر رفته است و فرآیند قادر به تولید مجدد قطعات با کیفیت است.
PPAP چارچوبی از الزامات را برای تامین کننده فراهم می کند تا اطمینان حاصل شود که طرح ها و نیازهای مشتری توسط تامین کننده قابل درک است. شبیه یک استراتژی کاری است. الزامات PPAP یک مذاکره مستقیم بین تامین کننده و مشتری است تا ثابت کند تامین کننده قادر به تولید تمام قطعات مورد نیاز برای برآورده کردن الزامات به طور مداوم است.
فرآیند PPAP تأیید میکند که تأمینکننده تمام مشخصات و الزامات طراحی مهندسی مشتری را درک میکند و این فرآیند میتواند به طور مداوم محصولی را مطابق با این الزامات در طول یک دوره تولید واقعی با نرخ تولید ذکر شده تولید کند.
فرآیند تأیید بخش تولید (PPAP) شبیه یک برنامه کاری یا استراتژی است. این مذاکره مستقیم بین مشتری و تامین کننده است که چگونگی رضایت از هر عنصر PPAP را تایید می کند. هر PPAP یکسان نیست، بنابراین قبل از پذیرفته شدن الزامات و شروع فرآیند باید مذاکره صورت گیرد. این تضمین می کند که هر دو طرف انتظارات یکسانی دارند. در بسیاری از موارد، تامین کننده یک گزارش مشخص مانند یک طرح کنترل، FMEA یا MSA خواهد داشت که به هدایت مشتری در فرآیند تامین کننده کمک می کند. در صورت قابل قبول بودن برای مشتری، بارها این اسناد کپی شده و مجدداً توسط تامین کننده استفاده می شود.
یک PPAP برای ارسال هر قسمت جدید و همچنین برای تأیید هرگونه تغییر یک بخش یا یک فرآیند موجود مورد نیاز است. برای مثال، اگر مشتری بخواهد یک قطعه موجود را اصلاح کند، باید یک PPAP درخواست کند. مشتری ممکن است در هر زمانی در طول عمر محصول درخواست PPAP کند. این امر مستلزم آن است که تامین کننده یک سیستم کیفیت را حفظ کند که همه الزامات ارسال PPAP را در هر زمان ایجاد و مستند کند. مشتریان در قبال ایجاد PPAP مسئولیتی ندارند بلکه تامین کنندگان مسئول آن هستند.
فرآیند تکمیل ارسال PPAP نسبتاً پیچیده است. این فرآیند مجموعه ای از عناصر کلیدی است که باید تکمیل شوند تا تأیید شود که فرآیند تولید؛ محصولی با کیفیت تولید می کند. همه عناصر همیشه برای ارسال PPAP مورد نیاز نیستند. الزامات خاص PPAP معمولاً در طول فرآیند مورد مذاکره قرار می گیرد.
الزامات ارسال PPAP معمولاً به پنج طبقه بندی یا سطح به شرح زیر تقسیم می شود:
سطح 1 – فقط ضمانت نامه ارسال قطعه (PSW) به مشتری ارسال می شود.
سطح 2 – PSW با نمونه های محصول و داده های پشتیبانی محدود.
سطح 3 – PSW با نمونه های محصول و داده های پشتیبانی کامل.
سطح 4 – PSW و سایر الزامات تعریف شده توسط مشتری.
سطح 5 – PSW با نمونه های محصول و داده های پشتیبانی کامل برای بررسی در محل تولید تامین کننده.
در اینجا 18 عنصر ارائه شده است که یک ارسال کامل PPAP خودرو را تشکیل می دهد، که از مستندات طراحی محصول عنصر 1 شروع می شود تا ضمانت ارسال قسمت 18 (PSW). همه اینها همیشه ضروری نیستند (به نیاز مشتری و پیچیدگی قطعه در حال ساخت بستگی دارد). بسیاری از ابزارها و تکنیک های تجزیه و تحلیل کیفیت شناخته شده جزء این عناصر هستند، این عناصر عبارتند از:
- مستندات طراحی: این شامل نقشههای فنی در کنار سفارش خرید میشود تا اطمینان حاصل شود که همه چیز هماهنگ و مطابق با الزامات است. اسناد طراحی باید شامل یک کپی از نقشه های مشتری و تامین کننده باشد. اسناد همچنین باید شامل یک کپی از سفارش خرید باشد. در برخی موارد تامین کننده ملزم به ارائه اسناد ترکیب مواد است.
- اطلاعیه تغییر مهندسی: اگر درخواست اصلاحات در یک بخش موجود باشد، اطلاعیه تغییر مهندسی مورد نیاز است. اگر PPAP به دلیل درخواست تغییر در یک قطعه یا محصول مورد نیاز است، اسناد درخواست و تایید تغییر باید در بسته PPAP گنجانده شود. این اسناد معمولاً شامل یک کپی از اعلامیه تغییر مهندسی (ECN) است که باید توسط بخش مهندسی مشتری تأیید شود.
- تأیید مشتری: تامین کننده باید مدرکی مبنی بر تایید توسط بخش مهندسی مشتری ارائه دهد. در صورت نیاز، نمونه های قبل از PPAP توسط مشتری برای آزمایش در محل سفارش داده می شود.هنگامی که آزمایش کامل شد، مهندسان آزمون یک فرم تأیید را برای درج در ارسال PPAP ارائه می دهند.
- حالت شکست طراحی و تجزیه و تحلیل اثرات (DFMEA): یک ارزیابی ریسک جامع که تمام خرابی های احتمالی در طراحی را ترسیم می کند. تجزیه و تحلیل حالت و اثرات شکست طراحی (DFMEA) یک فعالیت متقابل عملکردی است که ریسک طراحی را با بررسی حالت های احتمالی شکست و اثرات آنها بر محصول یا مشتری و احتمال وقوع آنها بررسی می کند. این حالت های خرابی عبارتند از: 1- خرابی محصول 2- کاهش عملکرد یا عمر محصول 3- مسائل ایمنی و مقرراتی DFMEA یک سند زنده است که باید در طول چرخه عمر محصول بررسی و به روز شود.
- نمودار جریان فرآیند: این نمودار تمام مراحل ایجاد قطعه را از ابتدا تا انتها نشان می دهد. نمودار جریان فرآیند کل فرآیند مونتاژ جزء یا مونتاژ نهایی را به صورت گرافیکی نشان می دهد. جریان فرآیند شامل مواد ورودی، مونتاژ، آزمایش، کار مجدد و حمل و نقل است.
- حالت شکست فرآیند و تجزیه و تحلیل اثرات (PFMEA): این به تمام شکست های احتمالی در فرآیند تولید نگاه می کند. حالت شکست فرآیند و تجزیه و تحلیل اثرات (PFMEA) تمام مراحل در فرآیند تولید را بررسی می کند تا هر گونه خطر بالقوه کیفیت فرآیند را شناسایی کند و سپس کنترل های اعمال شده را مستند کند. PFMEA نیز یک سند زنده است و حتی پس از تولید معمولی محصول باید به روز شود.
- طرح کنترل: اینها اقدامات پیشگیرانه ای هستند که برای کاهش احتمالات ذکر شده در PFMEA طراحی شده اند. طرح کنترل یک خروجی از PFMEA است. برنامه کنترل تمام ویژگیهای ویژه محصول و روشهای بازرسی مورد نیاز برای ارائه محصولاتی که به طور مستمر با الزامات کیفیت مشتری مطابقت دارند را فهرست میکند.
- تجزیه و تحلیل سیستم اندازه گیری: اینها مشخصات و جزئیات تمام تجهیزات مورد استفاده را ثبت می کنند.
- نتایج چیدمان: این یک بررسی اعتبار سنجی برای اطمینان از صحت اندازه گیری های روی نقشه در رابطه با نتیجه نهایی است. چیدمان ابعادی قطعات نمونه برای تایید اعتبار محصول مطابق با مشخصات چاپ مورد نیاز است. نمونه ها باید به طور تصادفی از یک دوره تولید قابل توجه معمولاً حداقل 30 قطعه انتخاب شوند. هر بعد در نقشه در مجموعه نهایی اندازه گیری می شود تا اطمینان حاصل شود که مطابق با مشخصات است. نتایج در یک صفحه گسترده ثبت میشود و در ارسال PPAP گنجانده میشود.
- طرح و گزارش تأیید طراحی (DVP&R): خلاصه ای از هر تست اعتبار سنجی انجام شده روی قطعه است. باید هر آزمایش انجام شده، شرحی از نحوه انجام آزمایش و نتایج هر آزمون را فهرست کند.این بخش همچنین میتواند شامل کپیهایی از تمام اسناد گواهی برای همه مواد (فولاد، پلاستیک و غیره) باشد که در چاپها فهرست شدهاند. گواهی مواد باید مطابقت با فراخوان خاص در چاپ را نشان دهد.
- کنترل فرآیند آماری: مطالعات فرآیند اولیه بر روی تمام فرآیندهای تولید انجام خواهد شد و شامل نمودارهای کنترل فرآیند آماری (SPC) در مورد ویژگی های بحرانی محصول خواهد بود. این مطالعات نشان می دهد که فرآیندهای بحرانی پایدار هستند، تغییرات نرمال را نشان می دهند و نزدیک به مقدار اسمی مورد نظر در حال اجرا هستند.
- مستندات آزمایشگاهی واجد شرایط: مستندات آزمایشگاهی واجد شرایط شامل گواهینامه های صنعتی برای هر آزمایشگاهی است که در تکمیل آزمایش اعتبار سنجی شرکت داشته است. این می تواند برای یک آزمایشگاه تست داخلی یا هر تاسیسات آزمایشی قراردادی خارج از محل باشد که برای تأیید اعتبار یا آزمایش گواهی مواد استفاده شده است.
- گزارش بازرسی تایید ظاهر: تأیید ظاهر (AAI) فقط برای اجزایی که ظاهر را تحت تأثیر قرار می دهند قابل اجرا است. این گزارش تأیید می کند که مشتری محصول نهایی را بازرسی کرده است و تمام مشخصات ظاهری مورد نیاز برای طراحی را برآورده می کند. الزامات ظاهری می تواند شامل اطلاعات مربوط به رنگ، بافت و غیره باشد.
- نمونه قطعات تولیدی: قطعات تولیدی نمونه برای تایید به مشتری ارسال می شود و معمولاً پس از تکمیل توسعه محصول در سایت مشتری یا تامین کننده ذخیره می شود. معمولاً تصویری از قطعات تولیدی به همراه اسناد مربوط به محل نگهداری قطعات در مستندات PPAP موجود است.
- نمونه اصلی: نمونه ای از نسخه نهایی محصول که نیاز به امضای مشتری دارد. نمونه اصلی؛ نمونه نهایی محصول است که توسط مشتری بازرسی و امضا می شود. بخش نمونه اصلی برای آموزش اپراتورها استفاده می شود و در صورت بروز هرگونه سوال در مورد کیفیت قطعه، به عنوان معیاری برای مقایسه با قطعات تولید استاندارد عمل می کند.
- بررسی وسایل کمکی: این لیست مفصلی از وسایل مورد استفاده در بازرسی تولید است. این باید شامل تمام ابزارهای مورد استفاده برای بازرسی، آزمایش یا اندازه گیری قطعات در طول فرآیند مونتاژ باشد. فهرست باید ابزار را توصیف کند و برنامه کالیبراسیون ابزار را داشته باشد. وسایل کمکی ممکن است شامل وسایل چک، کانتور، متغیرها و ویژگیها، مدلها یا الگوها باشد.
- الزامات خاص مشتری: این عنصر هرگونه درخواست خاصی را که توسط مشتری ارائه می شود را در خود جای می دهد. این عنصر از بسته ارسال جایی است که هر گونه نیاز خاص مشتری در آن گنجانده شده است.
- حکم ارسال قطعه: فرم ضمانت ارسال قطعه (PSW) خلاصه ای از کل ارسال PPAP است. یک PSW برای هر یک از شماره قطعه مورد نیاز است، مگر اینکه توسط مشتری بیان شده باشد. PSW شامل:1- دلیل ارسال (تغییر طرح، تایید مجدد سالانه و غیره) 2- سطح مدارک ارائه شده به مشتری 3- اعلام انطباق قطعه با نیاز مشتری 4- بخشی برای هرگونه توضیح یا نظر مورد نیاز ارائه شده است 5-امضای شخص مجاز تامین کننده به همراه اطلاعات تماس 6-محلی برای مشتری برای نشان دادن وضعیت PPAP
PPAP (فرایند تایید بخش تولید) یکی از اجزای APQP (برنامه ریزی پیشرفته کیفیت محصول) است .پنج مرحله برای APQP وجود دارد که فرآیند PPAP فاز 4 از APQP (برنامه ریزی پیشرفته کیفیت محصول) است. فاز چهارم APQP مرحله اعتبار سنجی محصول و فرآیند است.
در ظاهر، PPAP می تواند پیچیده به نظر برسد لیکن الزامات PPAP نشان دهنده نقطه اوج و گزارش فعالیت هایی است که هر تامین کننده “خوب” از قبل انجام می دهد. فرآیند PPAP صرفاً به قرار دادن گزارش فعالیت ها و نتایج آنها در قالبی ساختاریافته و منسجم کمک می کند.
برنامه ریزی پیشرفته کیفیت محصول (APQP) یک فرآیند تعریف شده است که برای معرفی یک محصول جدید در بازار یا ایجاد تغییرات در محصول پس از عرضه آن استفاده می شود. یک تیم متقابل کارکردی (CFT) متشکل از متخصصان مهندسی، تولید، کیفیت، تدارکات و توزیع، یک APQP را برای اطمینان از اینکه محصولات مطابق با نیازهای مشتری هستند، انجام می دهند.
فرآیند تایید بخش تولید (PPAP) یک استاندارد صنعتی است که فرآیندی را برای نشان دادن طراحی مهندسی و رعایت مشخصات محصول توسط فرآیند تولید تامینکننده مشخص میکند. از طریق PPAP، تامین کنندگان و مشتریان در مورد الزامات مورد نیاز برای دریافت تاییدیه قطعات تولید شده توسط تامین کننده توافق می کنند. اصول PPAP برای همه قطعات و کالاها قابل اجرا است، با ارائه یک فرآیند تأیید منسجم، به کاهش تأخیرها و عدم انطباق ها در طول تأیید قطعه کمک می کند. این به چه چالش(های) خاصی میپردازد؟
درک اطلاعات مورد نیاز برای اخذ تاییدیه قطعه را فراهم می کند و فرآیند تایید قطعه را استاندارد می کند.
نحوه اخذ تاییدیه قطعات/فرآیندها پس از تغییرات طراحی قطعه و/یا تغییرات فرآیند.
اطمینان حاصل می کند که قطعات ارسالی با اطلاعات مناسب و داده های کافی برای حفظ انطباق محصول ارسال می شوند.
یک رکورد از انطباق قطعه را ارائه می دهد.
جزئیات مربوط به سوابق طراحی را برای اطمینان از قابلیت ردیابی وضعیت طراحی قطعه در مبدا.
فرآیند تغییر محصول را کنترل میکند و یک خروجی مورد تأیید برای همه تغییرات فراهم میکند تا از انطباق با مونتاژ/فرآیند سطح بعدی اطمینان حاصل کند.
چگونه PPAP بر APQP تأثیر می گذارد؟
اگر نتایج PPAP انتظارات مشتری را برآورده نکند، معمولاً به این معنی است که فرآیند APQP به درستی کار نمی کند. آزمایش برای هر دو APQP و PPAP یک آزمایش تولید است. اگر محصول آزمایشی نهایی شامل قطعات معیوب باشد، سازنده باید زنجیره تامین را طی کند و بفهمد که کجای PPAP یا APQP اشتباه کرده است.
فرآیند تایید بخش تولید (PPAP) چارچوبی از الزامات مورد استفاده در زنجیره تامین برای ایجاد اطمینان در تامین کنندگان و فرآیندهای تولید آنها است.
هدف PPAP این است که اطمینان حاصل شود که طراحی مشتری توسط تامین کننده درک شده است و ثابت کند که تامین کننده قادر به تولید قطعاتی است که تمام الزامات را به طور مداوم برآورده می کند.
- این یک فرآیند کیفی کاملاً تعریف شده و پذیرفته شده است.
- در را به روی صنایعی مانند خودروسازی و هوافضا باز می کند.
- تایید توانایی تامین کننده
- درک نیازهای مشتری ایجاد یک فرآیند و توافق قابل اعتماد و قابل تکرار.
- کاهش هزینه و داشتن زمان سریعتر برای بازار
- حفظ انتظارات هر دو طرف.
- قطعات تضمینی مطابق با نیاز مشتری است.
- شواهدی از ثبات فرآیند.
فرآیند تولید اشتباه یا ضعیف (به عنوان مثال تجهیزات)
طراحی محصول نادرست یا مبهم
کیفیت مواد نادرست یا ناسازگار
کنترل کیفیت ناسازگار
هزینه ها می تواند سنگین باشد.
بسته به ساختار پایه و تجربه مدیریت کیفیت سازمان شما، تأثیر منابع برای ارائه PPAP می تواند سنگین باشد و نباید دست کم گرفته شود. با این حال، در میان مدت تا بلندمدت، مزایای پذیرش PPAP بسیار بیشتر از هزینه های منابع اولیه و آموزش است.
PPAP از فرآیندی که مهندسان ناسا برای پیشبینی بهتر خرابی تجهیزات پس از شکست سکوی پرتاب اولین مأموریت آپولو ایجاد کردند، تکامل یافت. یک آتش سوزی فلاش در ماژول فرمان 012 رخ داد که منجر به پارگی ماژول فرمان شد.
هدف از فرآیند ناسا جلوگیری از نقص عملکرد تجهیزاتی بود که باعث شکست آپولو 1 شد.
این فرآیند بیشتر توسط صنعت خودروسازی آمریکا به عنوان راهی برای سادهسازی و بهبود زنجیره تامین قطعات آن اصلاح شد. به طور خاص، گروه اقدام صنعت خودرو (AIAG) این سیستم را با برخی از ورودی های جنرال موتورز، فورد و کرایسلر توسعه داد.
اجرای PPAP ها در صنعت خودرو کمک کرد تا اطمینان حاصل شود که تامین کنندگان می توانند تعداد قطعات درخواستی را در یک بازه زمانی مشخص با قیمتی مشخص و در عین حال که تحمل سازنده را برآورده می کنند، ارائه دهند.
با گذشت زمان، سایر صنایع این روش را به عنوان وسیله ای برای تأیید درک متقابل برای عملکرد قطعات بین تأمین کنندگان و خریداران قطعه پذیرفتند.
فرآیند تایید بخش تولید PPAP
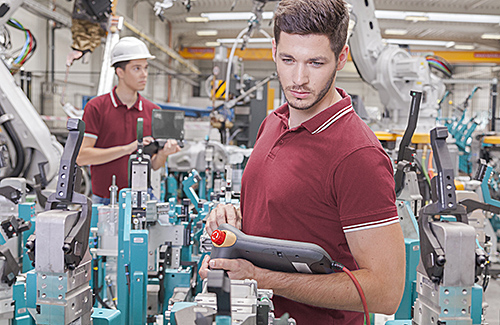
بدون دیدگاه